CLOSE
About Elements
田中贵金属是贵金属领域的翘楚企业。
支撑社会发展的先进素材和解决方案、
创造了这些的开发故事、技术人员们的心声、以及经营理念和愿景——
Elements是以“探求贵金属的极致”为标语,
为促进实现更加美好的社会和富饶的地球未来传播洞察的网络媒体。

The Challenges of TANAKA Precious Metals : Episode 3
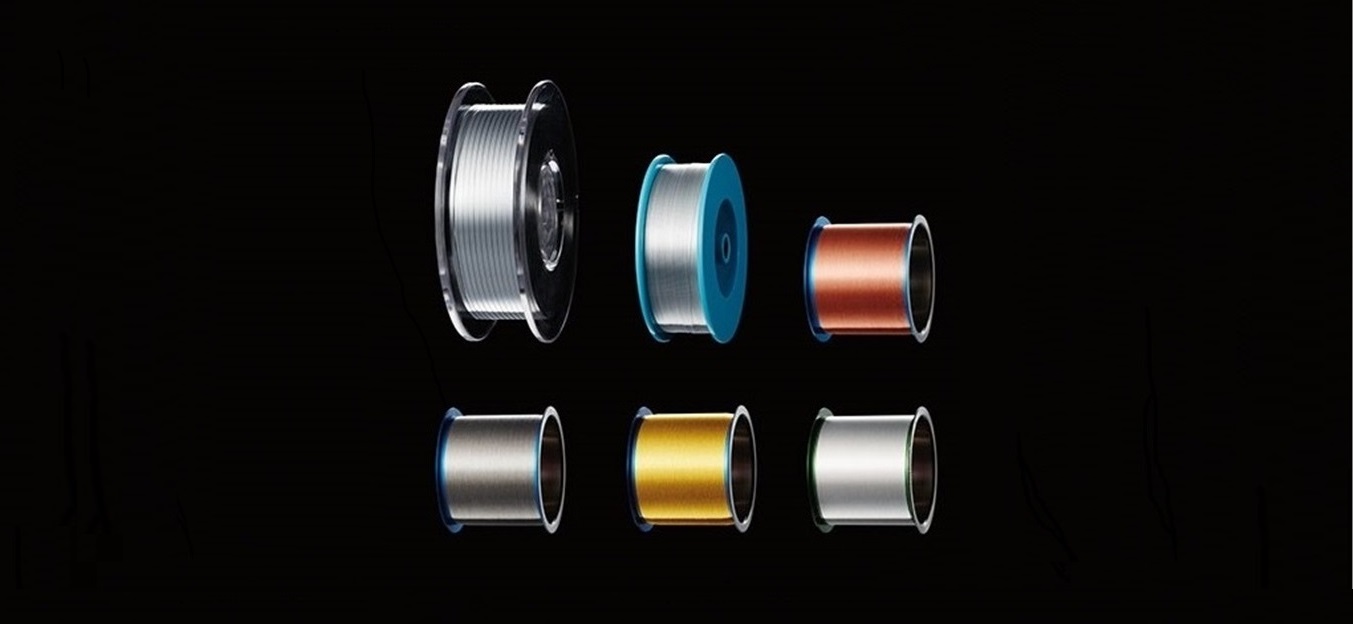
– Strategy for Rapid Expansion in Automobiles and Semiconductors –
(3)The strongest bonding wire
Mar. 1, 2021, Electronic Device Industry News
The semiconductor industry is maintaining its growth despite the COVID-19 pandemic. It grew by 5% in 2020 and it is expected to grow by 10% or more in 2021. The key factor of this growth is the large-scale investment in data centers in conjunction with the advancement of 5G high-speed networks. It is also spurred by the increase in telecommuting, the huge boom in game consoles, and the revival of consumer electronics. The semiconductor industry is expected to enter an unprecedented boom in the next few years as a result of the shortage of automotive semiconductors and the resurgence of smartphones in major markets.
“Under these circumstances, the production conditions for legacy processes such as the wire bonding process are becoming tighter compared to the most advanced flip chip and WLP in the semiconductor post-processing field. Some reports are saying that Taiwan ASE and other companies have ordered more than 1,000 units of wire bonders to increase their production capacity,” commented Masami Inaba, the Deputy Editor in Chief of Electronic Device Industry News.
Indeed, substrate companies in Japan, Taiwan, and South Korea are investing rapidly to increase production capacity, and the situation is becoming critical where there is a shortage of package substrates and wire bonders.
40% of the global gold market share, and expanding into copper
TANAKA Kikinzoku Kogyo has established a strong position in the field of bonding wires. In the 1950s, the company started development of a 10-micron-meter fine gold wire at the request of the then Ministry of International Trade and Industry (MITI). To establish a mass production system at the initial stage, TANAKA Denshi Kogyo was established as a joint venture with Mitsui Mining & Smelting. In the latter half of the 1970s, TANAKA Denshi Kogyo took a risk during the early stages of development of semiconductor bonding wire by developing overseas bases in Singapore and other countries and fully entered the market. TANAKA Denshi Kogyo (the domestic production base is the Saga Plant) currently handles the bonding wire business some 60 years after the start of mass production. The company has an overwhelmingly strong position in gold bonding wires with a 40% share of the worldwide market.
No. 1 in the world for bonding wire manufacturing
Mr. Isao Hirano, Director & Senior Corporate Officer of TANAKA Kikinzoku Kogyo, commented with confidence in an interview, “We have been providing reliable bonding wire products that accommodate the ever-evolving latest semiconductor technology. In addition to gold bonding wires, which is our specialty, we are expanding our comprehensive lineup of gold alloy, copper, aluminum, silver alloy, and aluminum-silicon products to meet customers’ applications.” Furthermore, the company is always paying attention to maintaining adequate supplies for customers and is constantly increasing capacity.
Gold bonding wire, which is known as the strongest bonding wire in the world, can be used for various forms of packages ranging from DIP to SIP, QFP, BGA, and FBGA. They are robust in stacked packages and ultra-thin packages. The use of high-strength gold allows a reduction of costs by using thinner wire, and it also can be adopted for fine pitch applications.
On the other hand, TANAKA Denshi Kogyo is also focusing attention on copper bonding wires that can result in cost reductions. The company is addressing approaches to strengthen proposals mainly for major OSATs and is pushing its technology to cut material costs by 90%. Furthermore, silver alloy bonding wires were commercialized and the number of applications is gradually increasing. The bonding properties of this type of wire are similar to gold while costs are similar to copper, and they are being used in LED packages in particular. TANAKA Denshi Kogyo also developed PCC wires that have copper coated with gold or palladium, which are used in a variety of packages as a low-cost version of the gold bonding wire. They are recently being adopted for automotive packages that require high reliability.
Full application of new technology for power devices!!
“The surge in data center investment is inevitable in the current situation. The issue, however, is power consumption. Data centers use more than 3% of the world’s total power, and there are predictions that use will increase up to 10% in the medium to long term. This will cause a bottleneck where there is a shortage of power. In such a situation, power control by power devices will be essential,” comments Mr. Akira Minamikawa, a well-known semiconductor industry analyst.
According to Mr. Minamikawa, new development for power semiconductors will also become necessary in the field of bonding wires.
For bonding wires to be used in power devices, TANAKA Denshi Kogyo has also been focusing on the development and mass production of highly reliable aluminum wires, thick copper wires, and other products. In particular, the company occupies more than half of the global market for thick aluminum wires, which is the de facto standard for IGBTs and other power semiconductor modules. TANAKA Denshi Kogyo holds almost 100% of the market share in Japan.
Thick aluminum wires are used as the main wiring material for the electrodes of power semiconductors such as IGBTs where TANAKA Denshi Kogyo has a wide product lineup with diameters ranging from 100 to 500-micron meters. The trend to adopt aluminum ribbon type bonding materials is growing among Tier 1 and finished automobile manufacturers. TANAKA Denshi Kogyo’s products are characterized by their rounded cross-sectional shape, which eliminates the generation of burrs during the ribbon shape forming process and enables manufacturers to maintain high productivity compared to products of other companies.
In addition to bonding wires, TANAKA Kikinzoku Kogyo is also focused on the development of sintered bonding materials for die-attach materials, and it is taking a company-wide approach to expand in the rapidly growing power device market. The Shonan Plant (Kanagawa Prefecture) is the production and R&D base for these products for power devices.
There will be no end for TANAKA Kikinzoku Kogyo in pursuing material composition technology to keep up with the advancement in customization of packages that require development to satisfy the performance, quality, and equipment specifications essential for latest technologies.
(Wataru Izumiya, Special editorial board member)
■Related Information
Products Information > Bonding Wires
TANAKA’s Technologies > TANAKA’s Precision Precious Metal Processing Technologies-Bonding Wires
Products and Solutions > Bonding Wires -New Possibilities Opened Up by TANAKA Denshi Kogyo, Holder of the World’s Top Market Share-