CLOSE
About Elements
田中贵金属是贵金属领域的翘楚企业。
支撑社会发展的先进素材和解决方案、
创造了这些的开发故事、技术人员们的心声、以及经营理念和愿景——
Elements是以“探求贵金属的极致”为标语,
为促进实现更加美好的社会和富饶的地球未来传播洞察的网络媒体。

Improving Durability Of Wire Bonds In EV Batteries
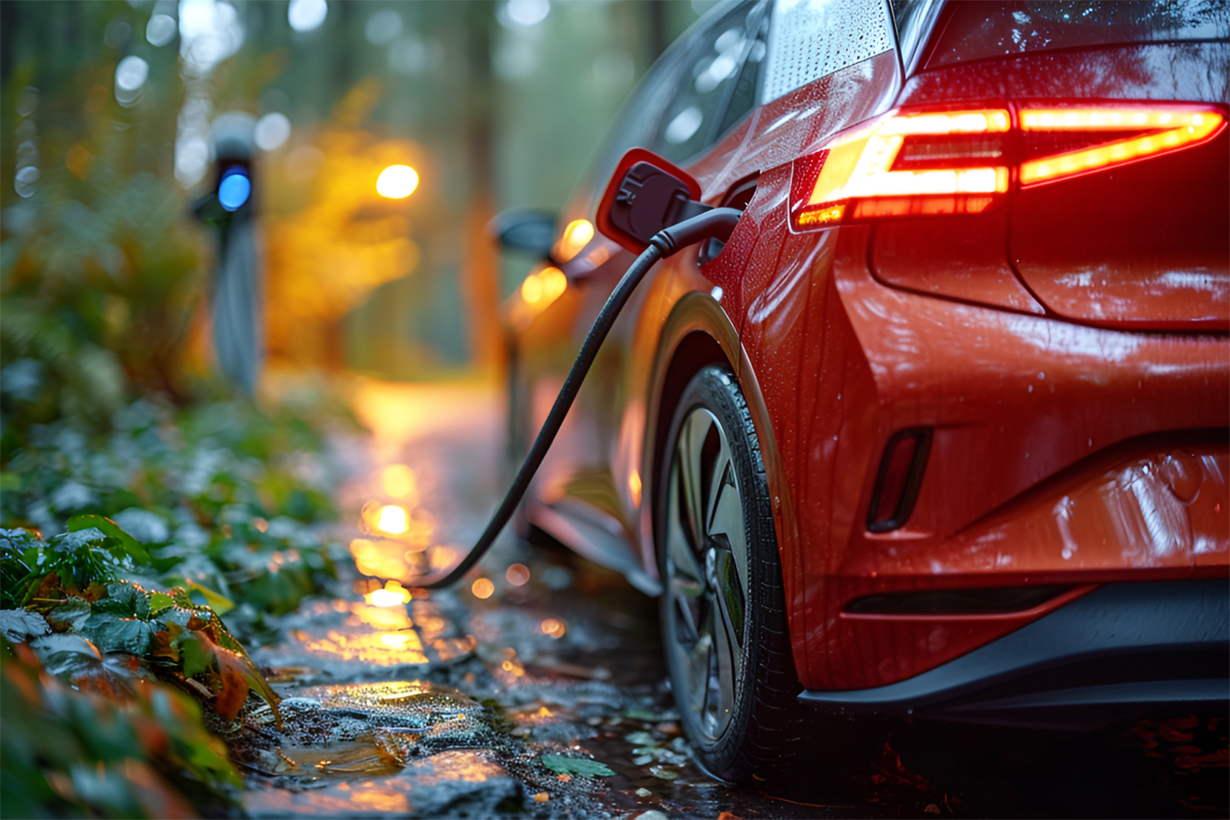
HOW2POWER TODAY
ISSUE: January 2024
Improving Durability Of Wire Bonds In EV Batteries
by Dodgie Calpito, Tanaka Kikinzoku International, San Jose, Calif.; and Shuichi Mitoma, Shizu Matsunaga, Kosuke Ono, and Tsukasa Ichikawa, Tanaka Denshi Kogyo, Tokyo, Japan
Wire bonding was developed and has long been used in semiconductor packaging because of its inherent flexibility and ease of programmability. These are the biggest advantages it has over other interconnecting methods. With wire bonding, electrical interconnections or wire bonds are created between the silicon die and its substrate using wires made of gold, aluminum, copper, silver alloys or palladium-coated copper composites.
Wire bonds are delicate with limited flexibility, and in semiconductors, they are usually encapsulated by buffer materials such as resin or mold compounds. These materials give them a measure of durability and strength to resist damage from vibration. But that measure of durability is lost in open-air applications in the majority of EV battery packs where there is no material to protect the wire bonds from the effects of vibration, leaving the wire bonds vulnerable to breakage.
In this article, we look at ultrasonic wire bonding as it is used for the interconnection of cylindrical lithium-ion (Li-ion) cells in EV battery packs. Specifically, we present a series of vibration tests that were conducted on wire bonds used in EV battery packs to determine the degree to which different aspects of wire bond design affect their susceptibility to breakage.
After discussing wire bond construction in EV battery packs and identifying the points of mechanical weakness, we introduce the test equipment that was developed to test wire bond vulnerabilities to vibration in this study. We then present the five comparison studies which we conducted to test the impact of vibration direction, material, wire shape, loop height, and single bond versus multiple wires.
The goal of these studies was to analyze the wire breakage problem in EV battery packs and to offer some mitigation solutions to reduce or eliminate the failure. After presenting the test results, we summarize the key findings that should help pack designers achieve greater ruggedness for wirebonds in EV battery packs.
Wire Bond Vulnerabilities In EV Battery Packs
Ultrasonic wire bonding is currently used for the interconnection of cylindrical Li-ion cells in EV battery packs. The negative wire is bonded to the cell rim while the positive wire is bonded to the cell center cathode that is additionally prone to vibration. The cell can is made of nickel-plated steel with the crimped rim having rounded cross-sections.
Wire bonds are designed for flat surfaces and bonding on the cells with rounded rims makes it even more challenging although later designs are now made flatter. The cell rim surface roughness is also inconsistent due to the crimping process and is prone to corrosion and electrolyte contamination.
Rough road conditions, rough handling or sudden acceleration/deceleration of the EV could cause wire fatigue and eventual breakage due to vibrations that are generated under such conditions. The result can be breakage in the heel region, the area between the bond and the span of the wire bond. This is a common cause of energy capacity loss in EV battery packs. Fig. 1 shows typical wire bonds interconnecting cylindrical battery cells together.
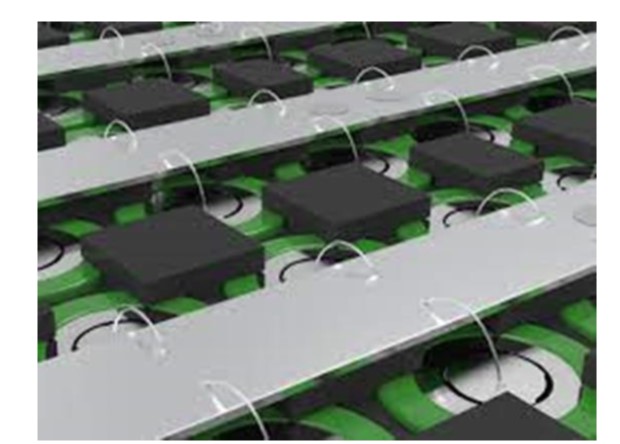