成功案例
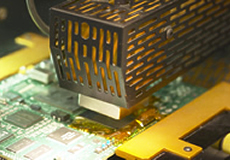
对制造装置的电镀加工
被认为已经达到极限的「生产性提升」与「成本削减」。
将生产线的停运压低至1/3的「电镀加工」究竟是?
半導体メーカーA社
市场正在显着扩张的半导体市场。在盛况背后,与海外厂商的竞争却是日益激烈,生产性的提升与成本的削减已成为所有相关公司的重要课题。靠着与以往相同的企业努力已经无法突破极限,找出新的方法解决课题是当务之急。
每年6 次的生产线零件交换,是仅存的削减成本的机会
半导体制造商A 公司希望趁着半导体市场恢复景气的这段时期,一口气取下市场占有率。为此,提升生产性并削减成本是重要的关键课题。A 公司至今也作了各样的相关努力,似乎所有能够能够改善的地方都已经彻底改善了。于是,A 公司为了实现更大幅度的生产性提升与成本削减,而成立了专案小组。
开发部门的T先生在加入这项专案后, 首先着手调查生产线的现况。调查开始后不久,T先生很快发现了一个问题点。那就是由于生产线每年需要停运6 次,因此无可避免地造成了生产性的降低。A公司的半导体制造过程中,必须经过以800℃ 高温加热的工程。由于过程必须用高温处理,因此制造装置本身也会承受负荷,导致装置内部的零件容易腐蚀与损伤。故此A公司必须定期停止生产线,并更换制造装置的零件。
为了更换零件而停止生产线的运转,这是A公司长年来希望改善的重要课题之一。虽然每次更换零件需要数百万日圆的费用,但若不更换零件则会导致半导体的品质明显降低。万一在半导体的成品中混入了不良品,将会导致客户的投诉,严重时更可能会发展成为影响A公司信用的重大问题。因此包含A公司经营团队在内的所有人,都认为停止生产线来更换零件是无可避免的必要程序。
对开发部门的T 先生而言,他的任务就是要找出能够超越以往的方法来提升生产性并削减成本。若是能够改善停运生产线时所造成的机会损失,即能够让这项专案成功。于是T 先生开始了他的挑战。
对制造装置本身施予「电镀加工」,使生产线的停运期间减至1/3!
开发部门的T 先生开始收集信息,挑战生产线的「生产性提升与成本削减」。参加半导体业界的展览会、研讨会,透过网络搜寻资料……,但却都无法从中获得有益的信息。当T 先生开始感到焦虑时,他从在别的案件中有来往的田中贵金属营业员口中,得知了一项信息。
「对制造装置施予电镀加工,就够提升装置的耐用性,并减少生产线的停运。」
当时,A公司已有委托田中贵金属进行钛电极的白金电镀加工,但却从来没有想过要对制造装置本身实施电镀加工。据田中贵金属的营业员所说,对于制造装置本身的电镀加工能够抑制装置的腐蚀与损伤,因此可以降低生产线停运的频度,且能够较以往还要缩短制造装置的停运期间。
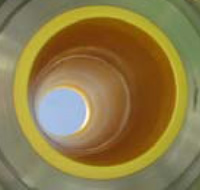
对制造装置的内侧实施10μm厚的镀金
对于从来没有想过的电镀利用方法,开发部门的T先生不仅感到惊讶,同时也对这项方法感到很大的期待。由于提案内容十分值得尝试看看,因此他努力地获得了管理者们的许可,并且委托田中贵金属进行电镀工程……。
在当时定期更换制造装置本身零件的情况下,生产线每年会有6 次需要停止运转。但透过这次采用的「只针对制造装置会达到高温的零件进行电镀加工」的方法,因为能够抑制制造装置的腐蚀与损伤,故能够将零件更换减少至每年2次,也就是原先的1/3次。不仅如此,成本也较原先需换零件6 次时降低了约40%。
实现了「生产性提升与成本削减」的T先生,顺利地使专案迈向成功。A公司也因此强化了企业竞争力,并在获取市场占有率的竞争中领先了其他对手公司一步。
田中贵金属的服务范围不只是将产品加工、交货就告一段落,更包含了回收再利用的过程。从已达到寿命的制造装置等废弃物中,或制造过程中产生的废料中回收贵金属,并将这些贵金属再次商品化,使其回到市场。T先生希望在下次更换装置时能够有效活动这些装置的镀金素材,因此正在考虑将回收再利用的部分也交给田中贵金属办理。